Creating custom metal parts is a critical process in various industries, from automotive and aerospace to electronics and consumer goods. Whether you need precise components for machinery or unique fixtures for your home, custom metal parts provide the tailored solutions necessary for specific applications. Companies like Jierui custom metal parts and custom service hardware are at the forefront of this field, offering expertise and advanced technology to meet diverse customer needs. This comprehensive guide will take you through the steps of making custom metal parts, highlighting essential aspects and key considerations.After that, non standard fasteners Not afraid of the future, dare to fight and fight, and won applause again and again in the market. https://jieruifasteners.com/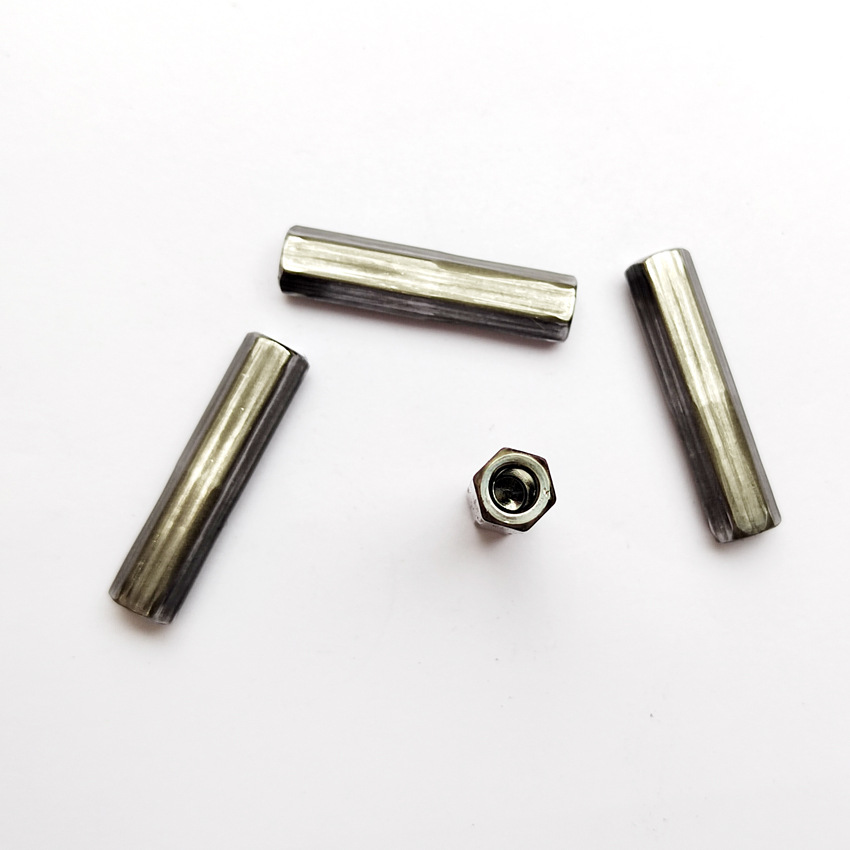
1. Key Considerations for Custom Metal Parts
Before diving into the manufacturing process, several factors need careful consideration:
Material Selection: The choice of material is crucial, as it affects the part¨s strength, durability, and performance. Common materials include steel, aluminum, brass, copper, and titanium. Each material has its properties, such as corrosion resistance, weight, and thermal conductivity, which should align with the intended use of the part.
Design Specifications: Detailed design specifications are essential for ensuring the part meets its intended function. This includes dimensions, tolerances, surface finishes, and any special features or requirements.
Manufacturing Method: Depending on the complexity and quantity of the parts, different manufacturing methods can be used, such as CNC machining, laser cutting, stamping, and welding. Each method has its advantages and limitations.
Cost and Lead Time: Custom metal parts can vary significantly in cost and production time. Factors influencing these include the complexity of the design, material choice, and manufacturing method. It¨s important to balance these factors to meet budget and deadline constraints.
Non standard hardware manufacturers.jpg
2. The Custom Metal Part Manufacturing Process
Creating custom metal parts involves several steps, from initial design to final production. Here is an overview of the typical process:
Design and Prototyping
The first step in creating custom metal parts is designing the part. This involves working with CAD (Computer-Aided Design) software to create detailed 3D models. The design should include all necessary specifications, such as dimensions, tolerances, and material type. Once the design is finalized, a prototype may be created using rapid prototyping techniques like 3D printing or small-scale machining to test the design and make any necessary adjustments.
Material Selection
Choosing the right material is crucial for the performance and longevity of the part. The material must meet the required strength, durability, and other specifications. Custom Service Hardware and Jierui Custom Metal Parts offer a wide range of materials, ensuring that the chosen material aligns with the intended application and environmental conditions.
CNC Machining
CNC (Computer Numerical Control) machining is a widely used method for creating custom metal parts. This process involves using computer-controlled machines to remove material from a solid block to create the desired shape. CNC machining is known for its precision and ability to produce complex parts with tight tolerances. It is ideal for both prototyping and production of custom parts.
Laser Cutting
Laser cutting is another popular technique for creating custom metal parts. This method uses a high-powered laser to cut through metal sheets with great precision. Laser cutting is especially useful for creating intricate designs and detailed features. It is also highly efficient, making it suitable for both small and large production runs.
Stamping and Forming
For parts that require specific shapes or forms, stamping and forming processes can be used. Stamping involves pressing a sheet of metal into a die to create the desired shape, while forming involves bending or shaping the metal. These processes are typically used for creating parts in large quantities due to their efficiency and consistency.
Welding and Assembly
If the custom metal part consists of multiple components, welding and assembly are necessary. Welding involves joining two or more metal pieces together using heat and pressure. Various welding techniques, such as MIG, TIG, and spot welding, can be used depending on the material and design requirements. Assembly involves putting together all the components to create the final part.
Surface Finishing
Surface finishing is an important step to enhance the appearance and performance of custom metal parts. This can include processes such as polishing, painting, anodizing, or powder coating. Surface finishing can improve corrosion resistance, wear resistance, and aesthetic appeal. Custom Service Hardware and Jierui Custom Metal Parts offer various finishing options to meet specific customer needs.
Quality Control and Testing
Ensuring the quality and accuracy of custom metal parts is crucial. This involves rigorous quality control and testing processes to verify that the parts meet all design specifications and performance requirements. Techniques such as coordinate measuring machine (CMM) inspection, hardness testing, and surface finish analysis are commonly used to ensure the highest quality standards.