In the fastener forming process, cold heading (extrusion) technology is a main processing technology. Cold heading (extrusion) belongs to the field of metal pressure processing. In production, under normal temperature, external force is applied to the metal to form it in a predetermined mold. This method is usually called cold heading.As an important brand soul of the company, Wedges Prestressed Cable Anchor Has outstanding performance, through the market test, still has a strong development trend. https://www.chinatianlong.com/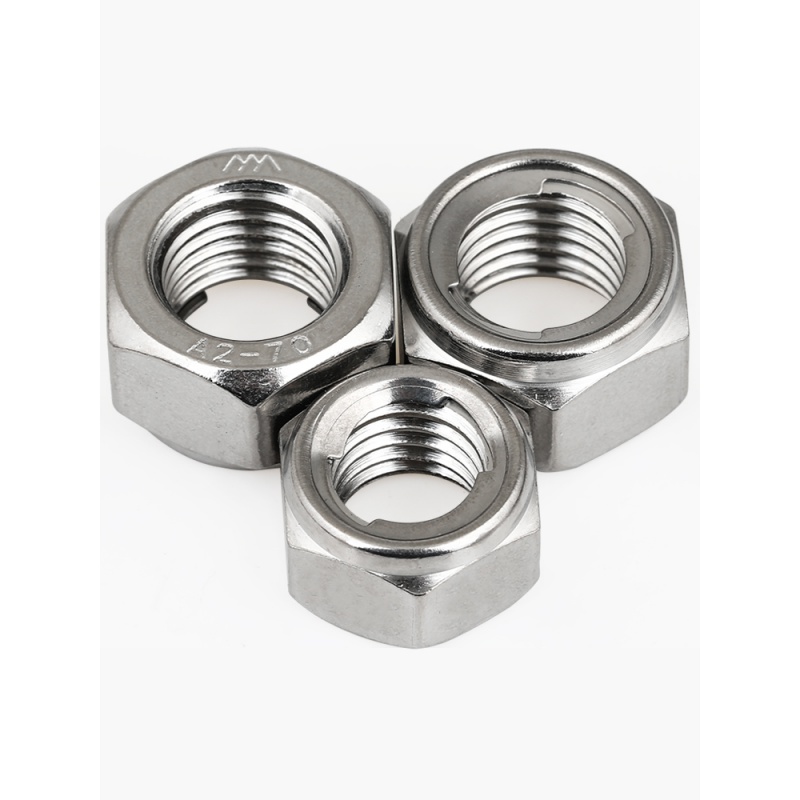
In metallurgy, the forging of materials heated above the recrystallization temperature (steel is about 700≧) is called hot forging.
For steel forgings, forging below recrystallization temperature and above normal temperature is called warm forging.
Figure 1 Forging temperature and common name
01
Advantages of cold heading (extrusion)
High utilization rate of steel: cold heading (extrusion) is a kind of machining method with little or no cutting, such as machining rod-type hexagon head bolts and cylindrical head hexagon head screws. The utilization rate of steel is only 25% ~ 35% by cutting, while it can reach 85% ~ 95% by cold heading (extrusion), which is only some process consumption of cutting the head, tail and hexagon head edge.
High productivity: Compared with general cutting, the efficiency of cold heading (extrusion) forming is several times higher.
Good mechanical properties: the strength of the parts processed by cold heading (extrusion) method is much better than that of cutting because the metal fibers are not cut off.
Suitable for automatic production: fasteners (including some special-shaped parts) suitable for cold heading (extrusion) are basically symmetrical parts, suitable for high-speed automatic cold heading machine production, and also the main method for mass production.
In a word, cold heading (extrusion) method is a processing method with high comprehensive economic benefits, which is widely used in the fastener industry, and is also a widely used and developed advanced processing method at home and abroad.
02
Cold forging process
Generally speaking, cold forging is to obtain the final shape of parts through the combination of various processes. Fig. 2 is an example of cold forging. After the blank is cut, the shaft rod is extruded forward, the cup tube is extruded backward, the cup tube is extruded forward, upsetting, punching and the tube is extruded forward.
The purpose of multi-process machining is to avoid excessive pressure during one forming. Because the fewer processes, the lower the cost. Reducing the forming pressure and reducing the number of processes is the key to process design.
Fig. 2 Example of cold forging process
03
Summary of main processing methods of cold forging
upsetting
Fig. 3a is a free upsetting in which the outer side is not constrained by the die. The machining pressure increases with the friction constraint. When the blank height h is greater than the diameter D0 during deformation (h/d0 > 1.0), C=1.2, but when the blank is thinned, C will rise to 2.5.
When the reduction rate increases, as shown in fig. 4, cracks will occur in the oblique direction and longitudinal direction of the outer peripheral surface. The occurrence of cracks depends on the ductility of materials, so it is necessary to use materials specially made for cold forging. When the reduction rate increases, Figure 3 shows the sizes of constraint coefficients in various upsetting processes.
Fig. 3 Constraint coefficient during upsetting
Figure 4 Upsetting crack
In free upsetting, when the initial height of the blank is more than twice the diameter, as shown in Figure 5, the blank is bent due to material instability, thus forming a folding defect. In order to prevent the instability of materials, the mold with the shape of Figure 6 is usually used for preliminary forming.
Figure 5 Instability
Fig. 6 Preliminary upsetting to prevent instability
Semi-closed forging
As shown in fig. 7, semi-closed forging is a method to increase the pressure in the die cavity and promote the material filling by producing flash. The technical big coffee is known in the Chinese screw net screw. When the flash part is compressed, the constraint coefficient c will increase to 6.0 ~ 9.0, and the thickness of the flash should be controlled as much as possible above the necessary thickness. Fig. 8 is an example of cold forging using semi-closed forging.
Fig. 7 Final stage of flash die forging
Fig. 8 Semi-closed forged products
Extrusion of shaft rod
Shaft extrusion is a processing method to reduce the diameter of material, which is usually called forward extrusion. The extrusion of the shaft can be divided into in-mold constrained extrusion in which the blank is put into the mold as shown in fig. 9 and free extrusion as shown in fig. 13b. Free extrusion is applied to forming with small machining degree.
(a) In-mold extrusion (b) Free extrusion
Fig. 9 The shaft rod is being squeezed.
As shown in fig. 10, internal cracking is easy to occur. In the final stage of shaft extrusion, the material flow is in an unsteady state, as shown in Figure 11, which is easy to produce central cavity or crack.
Fig. 10 Core extrusion crack Fig. 11 Unsteady extrusion defect
Cup-tube extrusion
The extrusion of cup and barrel is the most commonly used method in cold forging, which is to squeeze the punch into the material to form a cylindrical part with a bottom while the outer diameter of the blank is constrained by the die.
Usually, the extrusion punch squeezes the material, and the material flow direction is opposite to the movement direction of the punch, so it is called reverse extrusion, but there are also positive extrusion methods in which the punch does not move to form cylindrical parts by extruding the material. As shown in fig. 12,
Fig. 12 Back extrusion of cup shell
04
Cold forging method with compound drive
As shown in fig. 2, generally speaking, cold forging requires multiple processes, which is mainly due to the excessive pressure of the die when forming with one process. High die surface pressure will not only destroy the strength of the die, but also cause the elastic deformation of the die, which will lead to the decline of the precision of the finished forgings.
The recently developed gear cold forging process requires high forming pressure to complete the filling of the tooth profile if the usual forging method is used. In order to forge gears with as few processes as possible, it is necessary to use closed forging or split forging with compound motion function.
Closed forging
Fig. 15 shows the principle of closed forging and bevel gear forging. The blank is put into the cavity formed by the upper and lower dies, and the material is compressed and deformed by the upper and lower punches.
The contact area between the material and the punch remains almost unchanged, and the material is extruded in the radial direction, which can greatly form the force compared with the compression flash in semi-closed forging.
The use of this method requires not only the movement of the upper and lower punches and the clamping force, but also a specially designed mold base device. Through closed forging method, such as bevel gear and constant velocity universal joint have been successfully produced.
Fig. 15 The principle of closed forging and bevel gear forging.
Shunt forging
The principle of shunt forging is to design a space for material flow in both the main direction and the reverse direction of material flow, thus reducing forging pressure.
In the reverse extrusion as shown in fig. 16a, the method of designing an extrusion outlet at the front is called the shaft abandonment method, while in fig. 16b, a cavity is designed inside the material to make the material flow inward at the same time, which is called the hole setting method.
(a) shaft method (b) hole setting method
(a) convex shaft forming (b) split forging
Fig. 16 helical gear formed by shunt forging
This method is applied to the forging of gears by adopting a die with compound action. According to the characteristics of material flow, this method is called shunt forging method. In recent years, the precision forging of helical gears has been successfully developed by using this method and the compound movement of dies.