1. Introduction to Multilayer Flexible Printed Circuit Boards (FPC)The industry believes that, multilayer flex pcb The development of our company marks the rapid and steady progress of the whole industry. https://gekunflex.com/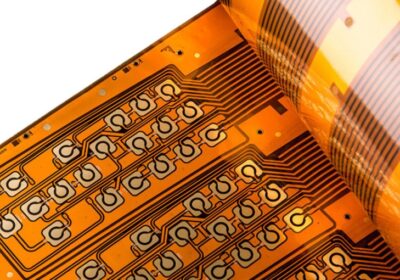
Multilayer flexible printed circuit boards (FPCs) are at the forefront of modern electronic design, providing both flexibility and durability in high-performance environments. These circuits are made up of multiple layers of flexible material, usually polyimide, which allows them to bend and fold while maintaining their electrical performance. As devices become more compact and complex, especially in automotive, aerospace, and medical applications, the demand for multilayer FPCs continues to rise.
In this article, we¨ll explore the manufacturing process of multilayer flexible printed circuit boards, highlighting their importance in key industries. We¨ll also emphasize the value of these boards in the European and American markets and how Gekun, a leader in FPC production, offers cutting-edge solutions.
Multilayer Flexible Printed Circuit Boards
Multilayer Flexible Printed Circuit Boards
2. Key Steps in the Manufacturing Process
Material Selection and Layer Construction
The manufacturing of multilayer flexible printed circuit boards begins with selecting the appropriate materials. Polyimide is the standard base material due to its high-temperature resistance and flexibility. Copper layers are added to create conductive pathways, and the number of layers depends on the complexity of the design.
Each layer is carefully constructed, starting with the outer flexible layer, followed by insulating and conductive layers in a sequence. The layers are aligned meticulously to ensure connectivity across all components.
Imaging and Etching Process
Once the layers are in place, the next step is to image and etch the copper to define the circuit paths. Photolithography techniques are used to project circuit designs onto the copper layer, which is then etched to remove unwanted areas. This step is critical to creating precise electrical pathways.
Layer Alignment and Lamination
After each layer is imaged and etched, the different layers are stacked and aligned using precision machinery. Any misalignment can cause failure in the final product, especially as the complexity of the multilayer flexible printed circuit board increases. The layers are then laminated using heat and pressure to form a single, unified structure.
Drilling and Plating
Once laminated, the board is drilled to create vias (small holes) that connect the different layers electrically. These vias are plated with copper to ensure proper conductivity between layers. The drilling and plating processes must be executed with high precision, as any defects can lead to failures in the finished product.
Testing and Quality Control
The final steps in the multilayer FPC manufacturing process involve rigorous testing to ensure electrical performance and durability. Automated optical inspection (AOI) systems are often used to detect defects, while electrical testing verifies the connectivity of all circuits. The quality control process ensures that the FPCs meet the high standards required for industries such as automotive, aerospace, and medical devices.
3. Benefits of Multilayer FPCs in Different Industries
Consumer Electronics and Automotive Applications
The flexibility and lightweight nature of multilayer flexible printed circuit boards make them ideal for consumer electronics, such as smartphones and wearable devices. They allow manufacturers to create compact designs while maintaining excellent electrical performance. In the automotive industry, FPCs are used in advanced driver-assistance systems (ADAS) and infotainment systems, providing both durability and flexibility in harsh environments.
Aerospace and Medical Device Markets
In aerospace, where weight reduction and reliability are critical, multilayer FPCs offer a solution that meets stringent industry standards. Their ability to function under extreme conditions makes them valuable in aircraft avionics. Similarly, in the medical device sector, FPCs are widely used in diagnostic equipment and implantable devices, where their flexibility and high reliability are essential.
Multilayer Flexible Printed Circuit Boards
Multilayer Flexible Printed Circuit Boards
4. Challenges in Manufacturing Multilayer FPCs
Complex Design Requirements
The design of multilayer flexible printed circuit boards presents significant challenges due to the need for precise alignment and electrical performance across multiple layers. Each layer must be carefully planned to ensure that the circuits are properly routed, and the design must accommodate the mechanical stresses that occur during bending and folding.
Reliability and Durability Concerns
In applications such as automotive and aerospace, FPCs are exposed to harsh conditions, including extreme temperatures and vibrations. Ensuring that the boards maintain their performance under these conditions requires advanced materials and manufacturing processes, which can increase production costs.
5. The Role of Gekun in Multilayer FPC Manufacturing
Gekun is a leader in the multilayer flexible printed circuit board market, providing high-quality solutions tailored to the needs of modern industries. With cutting-edge manufacturing facilities and a focus on innovation, Gekun offers FPCs that meet the most stringent industry standards. Their expertise in multilayer FPC manufacturing ensures that customers receive reliable, high-performance products suited for automotive, aerospace, and consumer electronics markets.
Gekun¨s commitment to quality and precision makes them a trusted partner for businesses looking to innovate and stay ahead in the competitive market.
Multilayer Flexible Printed Circuit Boards
Multilayer Flexible Printed Circuit Boards
6. Conclusion
The multilayer flexible printed circuit board manufacturing process is a complex yet crucial aspect of modern electronics. These boards provide the flexibility and durability needed for advanced technologies in automotive, aerospace, and medical industries. By understanding the manufacturing steps, benefits, and challenges associated with multilayer FPCs, businesses can better appreciate their value in the global market.
Gekun, as a trusted manufacturer, continues to lead the industry with innovative solutions that meet the demands of today¨s fast-paced technology landscape.